
For example while I can tell you what the specifics of “inertial coupling” are I really have no idea what a real aircraft would do as it moves through the air.

I’m not knowledgeable about actual aircraft I’m more a “I know some of the tech stuff” guy. Such propellers are more efficient than turbo-fans and their cruising speed, in the range of Mach 0.7–0.85, is suitable for airliners, but the noise generated is tremendous. In addition a large number of blades are used to reduce the work per blade and to maintain circulation strength contra-rotation is used. The maximum relative velocity is kept as low as possible by careful control of pitch to allow the blades to have large helix angles thin blade sections are used and the blades are swept back in a scimitar shape. The 'fix' is similar to that of transonic wing design. There have been efforts to develop propellers for aircraft at high subsonic speeds. There have been propeller aircraft which have attained speeds up to the Mach 0.8 range, but the low propeller efficiency at this speed makes such applications rare. As a result aircraft with conventional propellers do not usually fly faster than Mach 0.6. When the airflow over the tip of the blade reaches its critical speed, drag and torque resistance increase rapidly and shock waves form creating a sharp increase in noise. As the relative air speed at any section of a propeller is a vector sum of the aircraft speed and the tangential speed due to rotation consequently a propeller blade tip will reach transonic speed well before the aircraft does. This establishes a significant performance limit on propellers.Ī propeller's performance suffers as the blade speed nears the transonic. Increasing the number of blades also decreases the amount of work each blade is required to perform which limits the local Mach number. Using a smaller number of blades reduces interference effects between the blades, but to have sufficient blade area to transmit the available power within a set diameter means a compromise is needed.

Increasing the aspect ratio of the blades reduces drag but the amount of thrust produced depends on blade area, so using high-aspect blades can result in an excessive propeller diameter. Therefore a method is needed to alter the blades' pitch angle as engine speed and aircraft velocity are changed.Ī further consideration is the number and the shape of the blades used. Propellers are similar in aerofoil section to a low-drag wing and thus do not operate very well when at other than their optimum angle of attack.
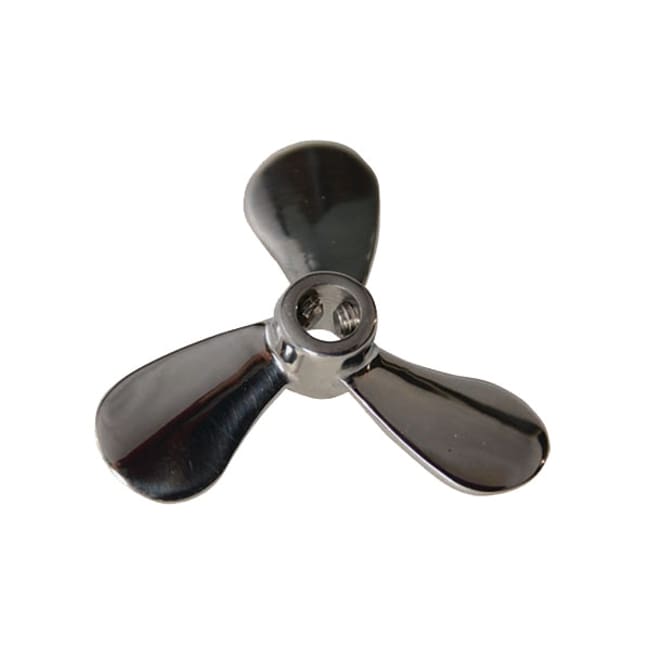
On the other hand, you want to stay with just a few blades if you could because (think of the propeller's blade path) more blades are more likely to get in the wake turbulence (or even sonic disturbance) of the proceding blade which reduces the ability to convert horsepower into thrust. Again the Spitfire is an example of a fighter where the 'working' altitude the propeller had to be designed for also increased significantly over its production life. A fighter that flies at high altitude has to have 'more propeller' than the same HP fighter that is limited to a lower altitude. The Spitfire had to have been a propeller problem since HP more than doubled from the Mk.I to the Mk.22/24, but the landing gears legs stayed short.Īnother issue is that the propeller has to be big enough to absorb the engine power at high altitude where the air is thin (low density). Getting bigger in diameter is usually a problem since diameter is limited by the landing gear length. When engines get more powerful there are only a few ways for a propeller to convert the increased horsepower into more thrust get bigger in diameter, wider blades or more blades.
